UltrawearPlus®
________________________________________________
UltrawearPlus®
Processed Automotive Rotor
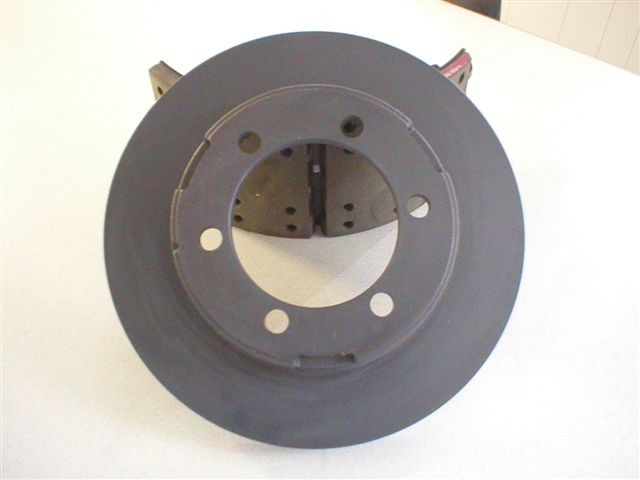
Road Test
-
UltrawearPlus®
Processed Brake Rotor
-
Installed
October 14, 1999
-
Five Michigan winters
-
Accumulated Miles 85,235
-
Original OEM Brake Pads
-
Average wear 0.003" from
original rotor
thickness
________________________________________________
UltrawearPlus®
Road Test, brake rotor at 85,235
miles

________________________________________________
UltrawearPlus®
Reduces Cost ~ Improves Quality
________________________________________________
Reduced Manufacturing Steps
________________________________________________
UltrawearPlus® ~ NRS
Advantage
________________________________________________
Quality Improvements
-
The combination of UltrawearPlus®
and
NRS
contributed to the following
-
Improved Corrosion Protection,
going from 72 hours with post paint to 120 hours with UltrawearPlus® Salt Spray test per ASTM B-117
-
Improved Shear strength with
NRS (no Adhesive)
________________________________________________
Examples of
UltrawearPlus®
Processed Backing Plates
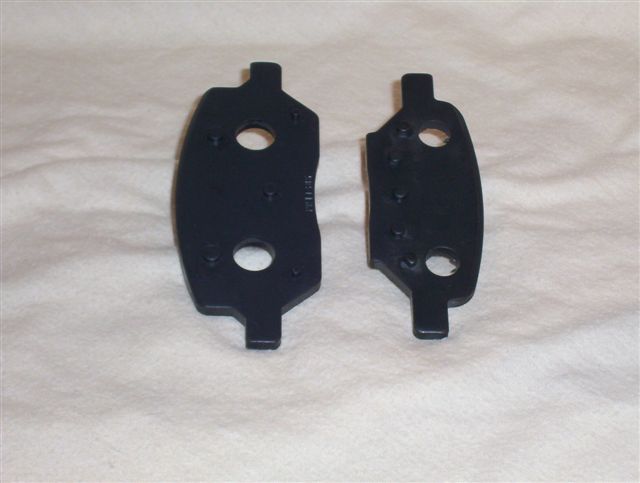
________________________________________________
Examples of UltrawearPlus® Red and
Black Pigmented Polymer Backing Plates with NRS
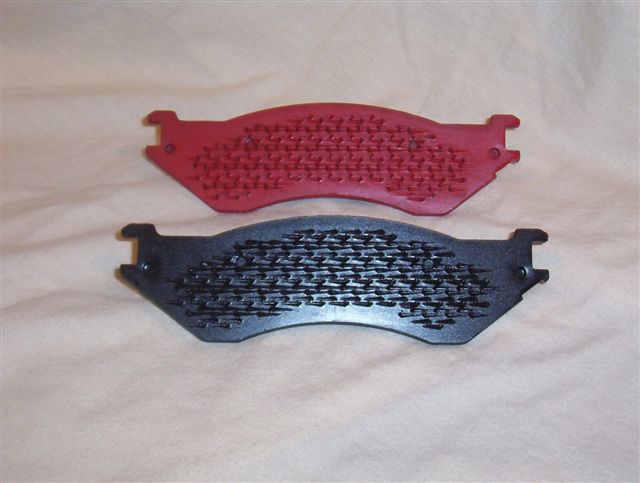
________________________________________________
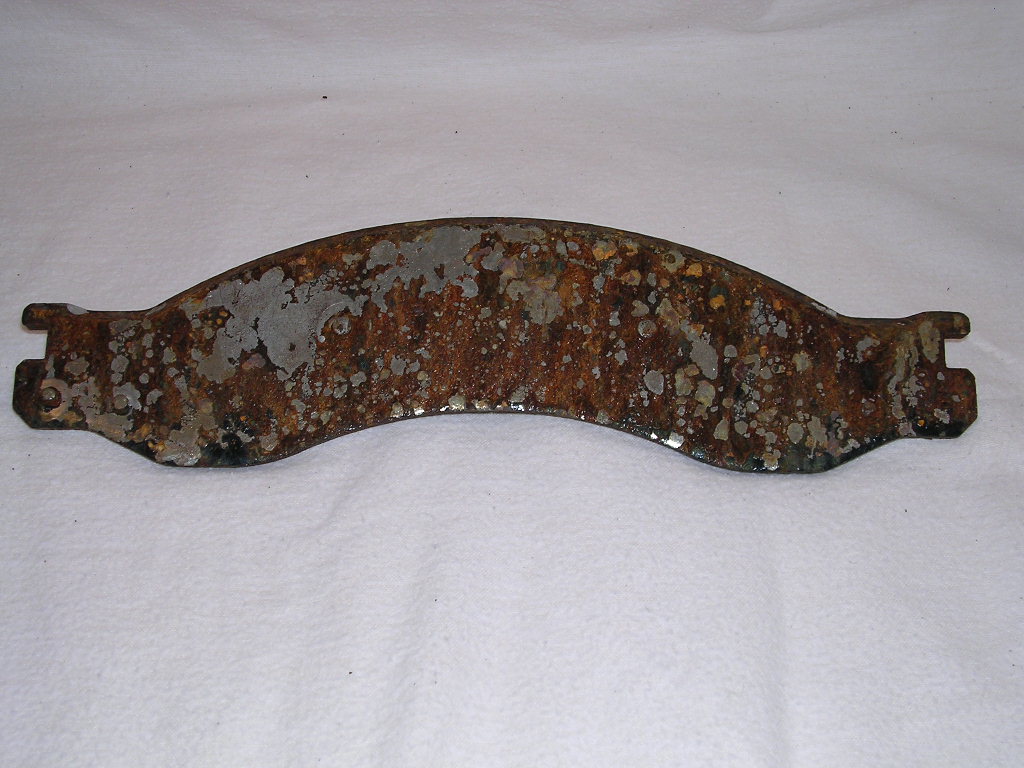
This brake backing plate on the left was
UltrawearPlus®
processed, then coated with black enamel paint and exposed to a 168
hour salt spray test per ASTM B-117, as you can see even though the
paint has washed away due to the salt fog exposure it still passed
the corrosion test with less than 10% red rust on critical surface
areas.
This
brake backing plate (right) was not
UltrawearPlus®
process it was washed then coated with the same black enamel paint
as the brake plate on the left, as you can see it failed the
corrosion test with 90% red rust.
This brake backing plate (left) was
UltrawearPlus®
processed then the friction material was molded onto the plate
(photo right) and the
UltrawearPlus®
clear polymer was applied. The plate was then salt spray tested
per ASTM B-117 for 240 hours, (notice no red rust on the ears).
240010.jpg)
|